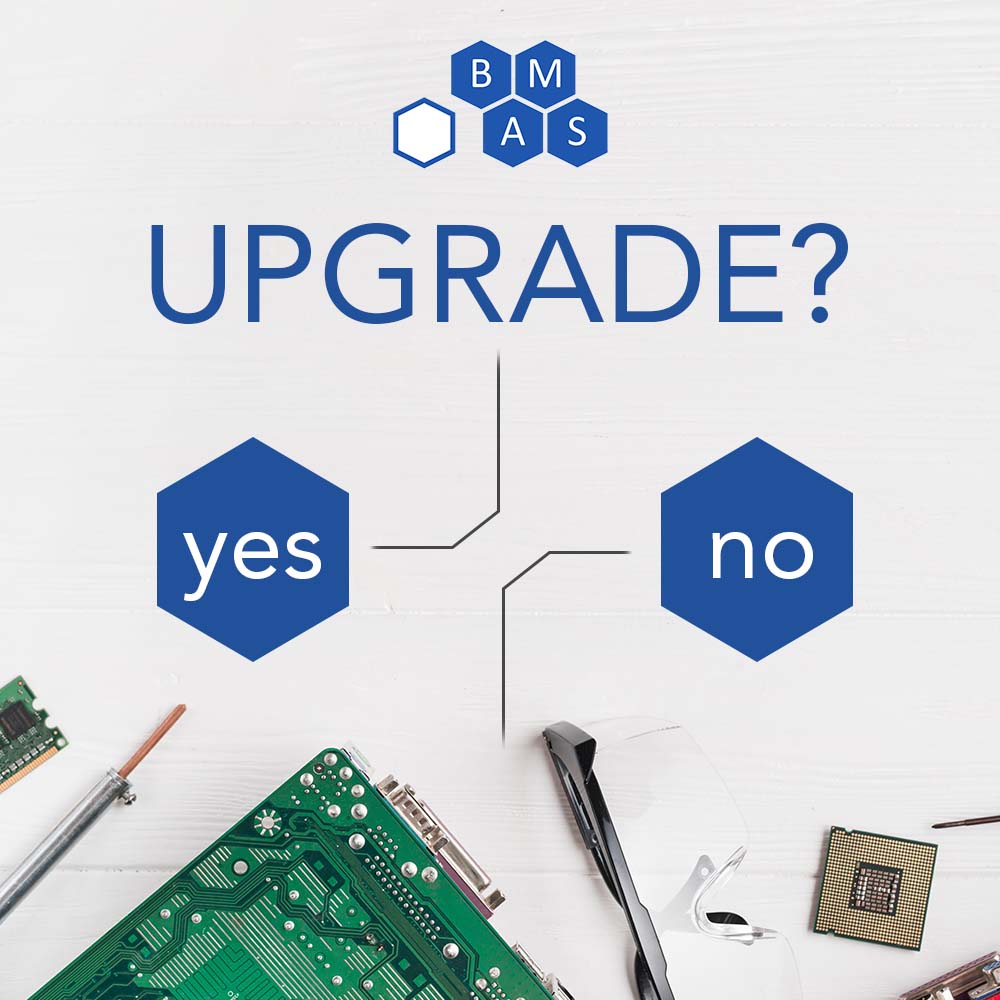
I get asked this question a lot. Nothing lasts forever, but nobody wants to spend money on something they don’t need. Any piece of automation ages – tooling wears out, belts break, bearings seize, but the control systems age in a unique way. Bearings and belts are governed by long-standing standards. People know what they are, how to maintain or replace them, and replacement parts are readily available for many years after the machine was built. Control systems, on the other hand, are evolving much more rapidly – better processors, more memory, faster and more convenient communications, and new programming standards. This brings innumerable benefits, but it makes long-term maintenance more difficult. The older parts aren’t made anymore, and few people know how to work with them. So, at what point does the age of the control system become a liability? When is it time to upgrade?
In the end, this comes down to personal comfort and confidence. The responsible party (plant manager, maintenance manager, production engineer) has to make the call. If the PLC fails, a VFD starts throwing faults, or the HMI elopes with your remote IO: Will you be able to get new parts? How quickly? Do you have access to the software, communications adapters, and expertise to load new programs or troubleshoot? Does the current system have all the functionality you need or want? Is it reliable? How costly is it if the machine doesn’t run for weeks or months?
Old but maintainable
An unusual example of this conversation: I spoke with a plant manager who oversees automation mostly comprised of Allen Bradley PLC-5 controllers. These are about 30 years old, are officially unsupported by Allen Bradley, and I’d typically recommend upgrading them. But this manager was very confident he could continue to maintain the system for the foreseeable future. He had plenty of spare parts stashed away, knew where to purchase more parts if needed, and had all the software and knowledge to support the system. In this case, it doesn’t seem like there’s a strong, immediate need to replace the system. The challenge is that this company was looking to add another station to the automation. It’s not easy to find contractors that want to build new systems with PLC-5 components, and this company didn’t have the resources in-house to do it, so the age of the system created a barrier to growth. I’d also argue that if the company ever lost that manager, it’d be in a tough spot trying to maintain the old equipment without his experience and connections.
Help!
A more common example: I often get calls about older equipment where the PLC died and there’s no recovery plan in place – no spare device, no backup program. Even worse, somehow these tend to be less common brands of components, so I don’t have the software or cables to connect to them, which generally makes support slower and more costly. This is a situation where the company waited to see how long the PLC would last. It’s a choice you can make, just know that you’re rolling the dice. For a simple machine, Breen Machine can sometimes complete an upgrade in 4 calendar weeks, with 6-8 being more common. Our customers often tell us others quote 16+ weeks on simple machines. A more complex machine will take longer. Can you afford to have your automation down that long?
Not dead yet
Another common example: A company recognizes that its automation is 30+ years old and wants to back up the PLC or upgrade the system before it’s too late. Hurray for being proactive! There are still some challenges when we get equipment this old, though. At that age, even a common brand of PLC isn’t common, and will probably need special connectors and software that we don’t have. Breen Machine builds relationships with local suppliers to get access to those things. A PLC of that age predates laptops. It was more common to have a hand programmer that looked a little like a calculator. There are PC programs to do the same thing, but they require old versions of Windows. And it’s comical the string of adapters needed for something that age – USB-to-RS232, RS233-to-some other serial in a big box, DIP switches for setting baud and parity bits. After we’ve got the program out of the PLC, there’s still a bit of work to do since there’s no automated conversion tool for a new PLC. It’s never too late for an upgrade, but the longer you wait, the more effort is required, and that means more cost
Which parts need upgrading?
Upgrades cost time and money, so we don’t want to mindlessly replace everything. We can be selective. Most of the electrical pieces – circuit protection, relays, sensors, motors, power supplies – can be readily replaced if there’s an issue, so I always focus on the pieces that can’t: PLC, HMI, servos, VFDs, IO. What if one of those parts breaks; can I upgrade just that part? Sometimes yes, but it usually makes sense to upgrade all of these parts at the same time. If one is obsolete, the rest probably are also. Newer parts also tend to follow different communications standards than older parts, so it makes sense to get them all talking on the same network.
General guidelines
The choice to upgrade or to wait isn’t always straightforward, but here are some guidelines to help you understand when/why an upgrade is the most cost-effective decision:
Upgrade:
- Parts are 20+ years old
- Parts are obsolete, hard to find, have long lead times
- Expertise and support aren’t readily available
- Equipment is unreliable
- Equipment needs additional functionality
- Adding new equipment that needs to “talk” with the old equipment
Don’t upgrade:
- Parts are readily available
- Expertise and support are readily available
- Equipment is reliable and performs all needed functions
Other resources
If you’re considering a controls upgrade, you may be interested in seeing what the process looks like and what other considerations come into play. Check out our other articles and videos related to this topic:
- Article: How to upgrade an obsolete PLC
- Video: Upgrading a SLC150 PLC
- Video: Choosing new hardware for SLC150 upgrade
- Video: Upgrading the program in a SLC150 upgrade
- Article: Upgrade or convert the PLC program
And don’t forget, we’re a resource as well! I personally visit almost every site where we’re considering a project so I can help you decide what makes sense. Give us a call or shoot us an email. We’re happy to help and quotes are free.
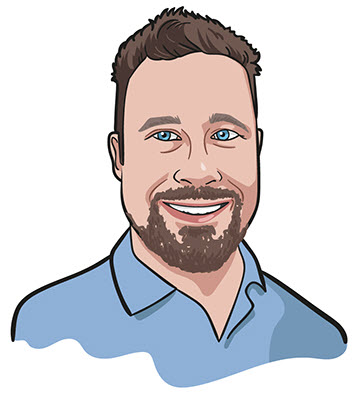
About the Author
Jon is an engineer, entrepreneur, and teacher. His passion is creating and improving the systems that enhance human life, from automating repetitive tasks to empowering people in their careers. In his spare time, Jon enjoys engineering biological systems in his yard (gardening).