Programming
“Software is a great combination between artistry and engineering.”
– Bill Gates
Programming is the unsung hero of modern manufacturing, extending far beyond just what the machine does. A well written program makes everyone’s life a little easier, supporting the operator with status and direction, maintenance with good structure and documentation, and management by simplifying training and tracking key data. Supporting the people that make your business profitable just makes sense, and we’re here to make that easy. We’re experienced at programming every aspect of automation in many industries. From packaging to assembly to inline measurement and beyond, we’ve got the sharp, friendly people to put your automation on the right track.
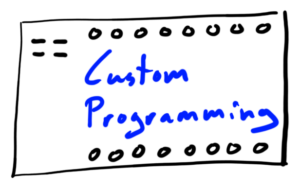
PLCs
The classical “brains” behind any automation is the PLC (Programmable Logic Controller). This is where the machine decides what to do and how. And no PLC program is complete without being able to detect fault scenarios and inform the operator.
These are traditionally programmed with Ladder Logic, and that’s still often true today, but today’s rigorous needs aren’t always well served by ladder. Modern PLCs support more programming languages and advanced features, sometimes being called PACs (Programmable Automation Controllers) in an attempt to capture the extra functionality. We’re fluent in many languages and can take advantage of all their strengths and mitigate their shortfalls. Check out our founder’s article at Control Engineering magazine online for more about the right language for the job.
We work with virtually any brand, leveraging our experience and industry resources to handle any project efficiently. Here are a few of the brands we’ve worked with:
PLC Upgrades
PLC programs from 20-30 years ago used different conventions than modern programs. Updating PLC hardware requires updating the program as well. We understand the old and the new, and can assure success in any upgrade project.
HMIs
The days of buttons and lights spread across a wall in the control room are mostly gone. Automation is much more powerful and feature-rich these days, and typically uses a touchscreen (the HMI or Human-Machine Interface) to add more depth and flexibility to the interface. But this interface shouldn’t reflect the complexity of the machine; it should simplify the operation and understanding of the process. A well designed HMI application is intuitive, giving the operator the right information at the right time, and organizing functions in ways that match the human’s approach to the job (not the machine’s program). Ideally, the HMI guides the operator effortlessly through the task of running the machine.
Modern HMIs go well beyond displaying information and accepting input. They can be used for data collection, display service manuals, and sometimes even perform the function of the PLC itself. Many HMIs are PCs at their core. Sometimes marketed as “Panel PCs,” they run an industrial, stable version of Windows, and can run almost any program imaginable.
Again, we pride ourselves in being versatile and using any brand you choose. Here are a few brands we’ve used in the past:
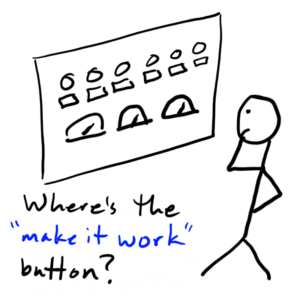
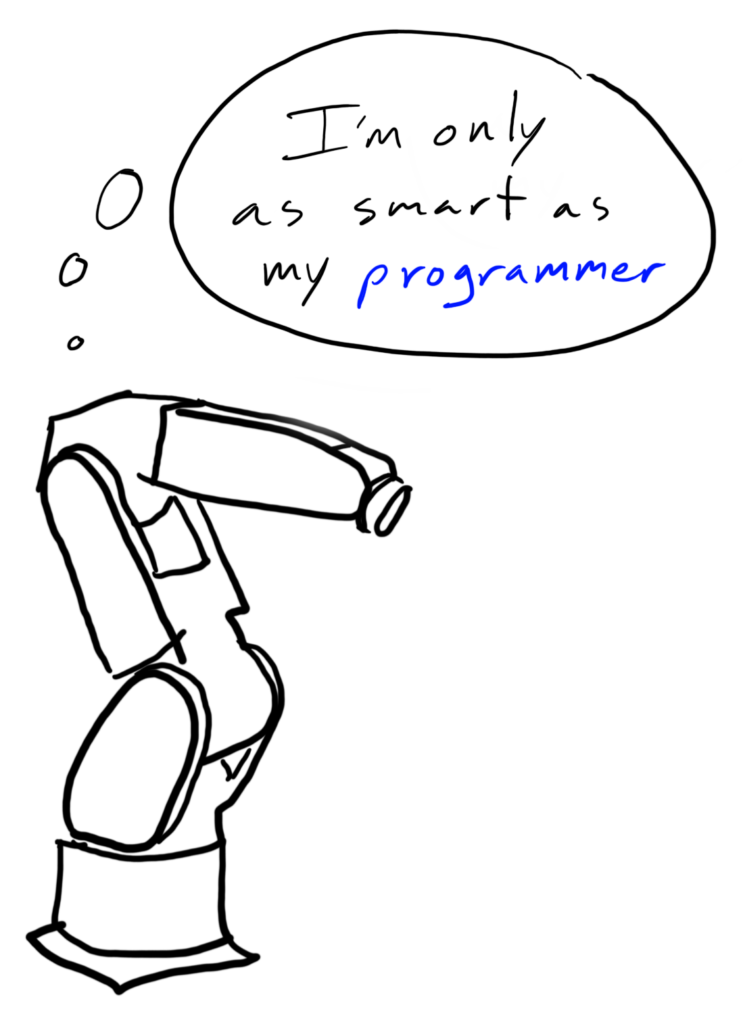
Robots
The most iconic and eye-catching part of automation, robots come in many shapes and sizes suited to many applications. They aren’t yet as intelligent as sci-fi novels would have you think, but they are improving rapidly in other ways including safety, reliability, and flexibility.
The buzz word lately has been “collaborative robots.” This is the latest set of safety standards, still rapidly evolving, that defines how a person can safely interact with a robot. This may involve a human and robot handing parts to each other or simply removing the need for guarding around the robot. There are certainly many advantages to a collaborative approach, but there are disadvantages as well, and in practice, the line between collaborative and not isn’t always clear. A robot can be bought that “is collaborative,” but if it’s implemented in a way that doesn’t follow proper safety, the resulting robot system still needs hard guarding and won’t be collaborative. On the other hand, a robot that’s “not collaborative” can be used without hard guarding if appropriate safety is considered. Don’t jump on the bandwagon without having an understanding of both.
Since robots are flexible and available off the shelf, they’re often a cost-effective replacement for custom pick and place hardware. They also offer a known reliable system compared to a custom design, a known cost for budgeting, and existing support resources.
And what robot programming section would be complete without pointing out some of the fancy features? Pick and place using a vision system, conveyor tracking, part data tracking, and multiple part types are all common and well within our experience. We’ve even worked with more tricky applications, like threading caps onto vials to a specified torque.
Here are a few brands we’ve worked with:
Motion
Discrete automation works by moving parts and tooling to fabricate, assemble, test, and package product. We have a whole spectrum of options to control that motion, ranging from simple VFDs (Variable Frequency Drives) to high-performance servos. Most OEMs will focus on one or the other for all motion, trying to stick with their company’s canned solution. However, simple or cost-sensitive applications can often benefit by blending approaches from the two ends of the spectrum. We have the experience to guide your decisions, the open-mindedness to find the right solution for your application, and the programming expertise to make it all work.
Here are a few brands we’ve worked with:
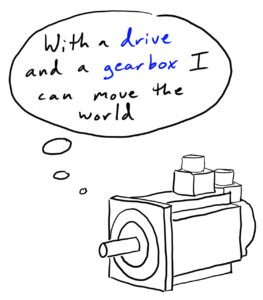
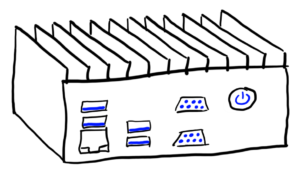
PCs
Automation is increasingly expected to do things that PLCs aren’t good at – database integration, complex math, advanced quality control, extending peripheral functionality, custom communications. PCs, similar to your laptop or desktop at home, are the answer to these challenges. They’re powerful and supremely flexible, offering many pre-built libraries of code that bring valuable features within grasp. Yet, despite the incredible promise of PCs in automation, most controls engineers aren’t familiar with their use or programming. They may remember the early industrial PCs (IPCs) that were known to be unreliable due to hardware failure and software crashes. Today’s IPCs have no moving parts, are built to withstand harsh environments, and run on stable operating systems. They’re very reliable.
Don’t overlook PCs for your automation challenges. Often they enable the functionality your process needs that people tell you is impossible. We have a strong background in PCs, servers, and databases, as well as the typical industrial automation. We’ve programmed PCs for:
- AI/ML (artificial intelligence/machine learning) vision processing
- custom communication protocols
- custom 3D vision applications
- custom OPC implementations
- database integration
Let’s find new ways to solve your most challenging automation needs together.
Automated Inspection
More and more, we see manufacturers that demand perfection and big data. Suppliers to those manufacturers are often faced with tough inspection standards, even losing the contract from 1 defect in a million. Humans can’t keep such standards. They get bored with monotonous tasks, missing defects, and can’t inspect high volumes of parts. This is the perfect opportunity for machines to shine.
Automated inspection is increasingly used to ensure part quality and collect a bevy of part information to guide manufacturing and management decision makers. These systems often employ smart sensors (sensors with programming built in) like cameras and laser profilers for 2D or 3D vision. Other times, measurement devices with limited smarts (laser micrometers, pressure sensors, etc) are combined with the programmability of a PLC to create a quality measurement system.
In 2D vision, the tools are often easy to use, but applications can still benefit greatly from the intuition that comes with experience. There are so many soft variables to consider. We’ve worked with several brands and many varieties of application, from measurement to presence/absence to defect detection to OCR to robot guidance. Check out our founder’s article on vision inspection at Control Engineering magazine online.
Measuring a third dimension with laser profilers or structured light cameras adds a lot of power to inspection. We can measure more features at a time, get around tough lighting challenges, measure all the way around objects, and measure features invisible to a 2D system. But, as you’d expect, this comes at the cost of greater complexity, and the built-in tools haven’t gotten smart enough to cover all the applications as easily as 2D tools do. We’ve got a lot of experience developing custom applications to cover the gap, and since we’re usually developing on a PC, we get a lot of other options for minimal additional effort: datalogging, custom displays, remote connectivity, statistical analysis, and basically anything you might need. Check out our case study on custom 3D inspection.
Here are some of the vision brands we’ve worked with:
Of course, there are many other ways to test and measure products and processes – leak testing, thickness, automated product calibration. We’ve got experience with a variety of applications, and we’re always doing new and exciting things. Let us know if you see a need we might help you fill.
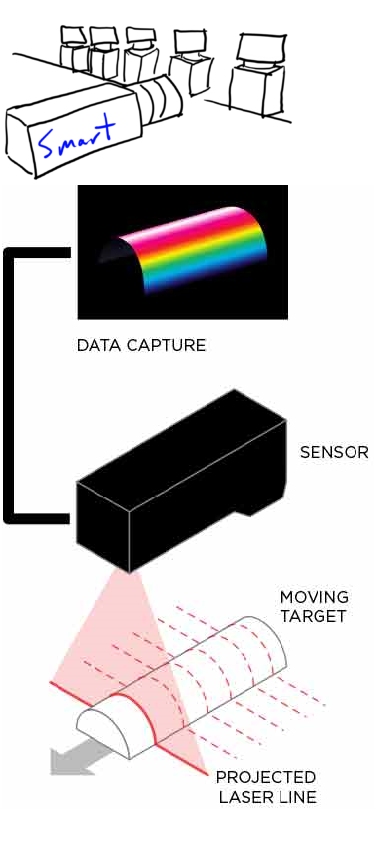